Back to Don's Maps
Bâtons Percés
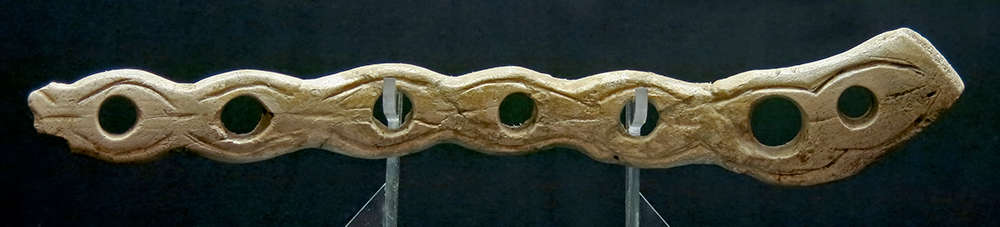
This unusual bâton percé from le Souci, Lalinde has a row of eight holes of different sizes.
Photo: Don Hitchcock 2015
Source: Musée d'Art et d'Archéologie du Périgord, at Périgueux
Les bâtons percés : décors énigmatiques et fonction possible
Translation: Don Hitchcock
Identified as early as 1866, the pierced bâton has produced no less than 37 hypotheses regarding its use. Among the most often expressed uses was that of a spear head straightener, in combination with heat from a fire. On some of the artefacts traces of use, sometimes two by two, evoke the twisting of a cord through the hole.
After observing scroll like decorations, the author at first fabricates varied pierced bâtons and then experimentally takes on the 'use with cord' hypothesis. Proved efficient, this last experiment is a possible explanation of some ornaments but the traces of use obtained are different from the archaeological tools. 75 % of the pierced bâtons that are left to us are broken. The small fragments found with them confirm the domestic use of the artefact, but the shape of some of the breaks forces us to look for another way of breaking.
Experimentation opens the way to the use as a cord securement attached to weights which reproduces under heavy loads or strong impacts, all the observed archaeological breaks and it may give another tentative explanation of the so-called phallic ornaments.
Note that throughout this paper, the author refers to a 'sagaie' in the original French, which is often translated as a spear, spear head, or dagger. The object referred to in this case is a spear head, normally made of ivory or bone or reindeer antler, and is a relatively short piece of equipment lashed (and often glued as well) to a much longer spear shaft. The author seems to think that the pierced bâton originally called a 'bâton de commandement' was used to straighten the sagaie.
I believe that this is supposition is in error. The maker can easily choose a piece of bone or antler and cut a perfectly straight spear head from it. The raw materials were not in short supply, and the maker could pick and choose from a range of suitable unprocessed bones or antlers. There is no need for straightening, and in fact this would be an extremely difficult task should it be attempted, unless the spear head was first hafted onto the shaft, which would then give the leverage required, though it would be a big test of the strength of the hafting process.
However it would also be possible to soak the bone or antler or ivory in water to make it possible to remove more easily any remaining lack of symmetry because of bending in the spear head, if the spear head was taken from a curved section of the bone or antler.
I believe that it is far more likely that the pierced bâton was primarily used for straightening the spear shaft, made of wood, as well as acting as a 'gauge' to ensure that the shaft was uniform in diameter. The raw material is often a very thin, whippy sapling or branch with at least one pronounced curve, and possibly with several changes of direction, which must be removed to create a long, straight, thin shaft suitable for accurate casting by the spear thrower. The raw materials for spear shafts must have often been very hard to come by in the periglacial conditions extant at the time and place where pierced bâtons and spear throwers are common, and the hunter must have been prepared to make the best of a bad job, and use whatever was available, and make it work well.
Shafts must have had to have had protruding bumps taken out, and possibly thinned down to a uniform diameter over much of their length. Spears for casting with a spear thrower are more properly referred to as darts. They derive much of their effectiveness and efficiency by being as uniformly thick as possible, and thin enough that when thrown, they first bend quite considerably under the force applied to them to overcome inertia by the spear thrower, and they then turn that potential (bending) energy into forward motion as they straighten, and 'kick' off the end of the spear thrower as it reaches the end of its arc. - Don
Bâton percé sculpted in the shape of an ibex.
Facsimile
Photo: Don Hitchcock 2015
Source: Display, Musée d'Archeologie Nationale et Domaine, St-Germain-en-Laye
If there is one object that has spilled more ink than anything else in archaeology, it is the enigmatic pierced bâton, first described in 1866, under the name of 'bâton de commandement'.
Sometimes sumptuously adorned with animal or human figures, sometimes covered with signs apparently present throughout the Upper Palaeolithic, it is indecipherable, and sometimes devoid of decoration, it is rare in the Solutrean, reaches its apogee in the Magdalenian, and seems to disappear in the Badegoulian.
By turns interpreted as a hunting trophy, ambisexual instrument, tent peg, and more recently a boomerang or a fire drill, Glory (1959) offers five classification categories:
1. theories based on psychological probabilities;
2. theories based on similar objects used worldwide;
3. theories based on wear or decorative patterns;
4. theories based on experimentation drawn from ethnological facts;
5. theories based on experimentation and from ethnology, but with the inclusion of traces of wear.
Peltier (1992) used just three classifications:
• non-utilitarian objects;
• utilitarian objects: tool, utensil;
• utilitarian objects: weapon.
The thirty-seven hypotheses of use issued to date alone testify to our ignorance about a piece of technology which at first sight has a simple design, and encourages researchers to retain only those:
a) that draw their origin in ethnology;
b) whose experimental reconstitution results in a feasibility, efficiency and causes some traces of use identical to that observed on prehistoric pieces.
In recent publications, only two hypotheses are often used: spear head straightener and sling handle for throwing spears.
The Spear Head Straightener hypothesis
The hypothesis was discussed many times since the late nineteenth century, but Leroi-Gourhan (1943) seems to have been the first to use an experimental reconstruction of a bâton percé to straighten bone spear heads (but not of reindeer antler, oral communication dating from 1976).
Dating from that time, in publications on prehistoric themes, the explanation of bâtons percés as straightening tools on 'hot' spears was accepted without objective criticism and without understanding the phenomenon.
Therefore, in prehistoric publications, straightening says 'hot' spear heads flourished without genuine concern for objective criticism and sometimes without understanding the phenomenon.
It now appears likely that we we were, like others perhaps, the victims of a number of facts or statements of fact such as:
• the scientific aura of the 'expert' (Leroi-Gourhan);
• misinterpretation of the term 'hot';
• a lack of original documents, whether in key publications such as those concerning Inuit straighteners or genuine archaeological pieces;
• the sheer number of images or drawings accompanying the older publications;
• a shortage of the essential raw material, i.e. reindeer antlers.
Leroi-Gourhan, like other leading scientists, had so much left his indelible mark on the world of prehistory and prehistorians that he had become for many of us, the inescapable 'reference', and his assumptions were sometimes considered as incontestable truths.
Thus in 1986, after writing our article on decoration and function, J. Allain did not immediately support our premise for fear of upsetting the ideas of his master. Yet he had foreseen the interest of such an approach by writing:
'Careful examination of such a rich and diverse selection of bone pieces is able to provide useful additional information on the equipment of the Magdalenian hunters' (Allain, Rigaud, 1986).
Straightening using heat
Straightening using heat was part of our peasant childhood and we often used it to make straight bamboo rods used as fishing poles. It was heated, by rotating between the fingers over a flame. The part of the stem closest to the nodes momentarily gained some flexibility.
After bending between thumb and forefinger of both hands, on the knee or on the edge of a table for poles of larger diameter, we only had to wait for the bamboo rod to cool to retain the form we had imposed, and for the natural flexibility to return.
Never, however, did we have need of a straightener. We never worked with fallen antler or antler taken from a dead animal, but Peltier (1992) used this straightening technique by heating spear tips on the edge of an experimental fireplace.
Most spear heads, sagaies, from La Garenne (Saint-Marcel, Indre) are made from rods taken from large dropped male reindeer antlers, and more rarely on fresh antler from hunted animals. Was the freshness of dropped antlers a criterion for choice? We will likely never know.
Averbouh et al. (1999) think 'that in the vast majority of cases, the Magdalenian - if not others - fresh antler was carved 1-2 months after its fall without special treatment'. Our experiments lead us to see that it is possible to carve reindeer antlers several years after its fall, whether kept moist or not.
Often we moisten, usually with saliva, one of two grooves while we carve the other, in order to soften a few tenths of a millimetre of material. It is also possible to dip the tip of the burin in water every three or four passes.
The latter method has the advantage on the one hand of avoiding dulling of the cutting edge, and on the other softens the work surface without soaking, which solves the problem of obtaining a container for large pieces of antler.
The marks of carving are then perfectly comparable to those observed in the gisements. This is, in our opinion, much more of a chisel sharpening problem that needs to be shaped and sharpened to both cut the groove deeper, and to widen it, without having to change tools to perform both actions.
Even so, reindeer antlers which have totally dehydrated are not able to be worked by heat. The action of heat makes the antler more brittle, which we learned the hard way when straightening a spear in our first attempt, which broke like glass in our fingers.
In order for it to attain a certain flexibility, it is essential to soak the reindeer antlers in water. Peltier (1992) uses hot water, but this is not mandatory and cold water is ideal, it is only a matter of more time spent soaking.
After correction of the curvature, heat is only needed to accelerate the elimination of excess moisture. This drying can be achieved in two or three minutes over a high heat, or after several hours or even a day at room temperature. A straightened spear point (sagaie), abandoned outdoors while being protected from the rain, resumed its original curvature after a month and a half. Among modern techniques hair styling offers similarities with straightening spear points.
The curling iron, whose technique seems to go back to the Assyrian civilisation, was adopted by all ancient civilisations and lasted until the 1800s. Preheated on a fire, the curling iron was used on dry hair (or whiskers) for sharply curved patterns. Now we practice styling, or, conversely, straightening. Hair, previously wet, is either wound on curlers or stretched and dried. The hair dryer only accelerates the drying process and drying at room temperature is quite possible. As with spear heads, hair that is blowdried more quickly resumes its natural form when air humidity is high.
Being economical with reindeer antler
After twenty-five years, re-reading what has been written on the subject, perhaps we too have the impression that shaping a spear necessarily involved the phase of straightening. Recent contradictory observations allow us to doubt this.
Despite the substantial deliveries from J.-F. Le Mouël, our supplier, we have always used reindeer antler from l'île de Banks sparingly. This relative shortage of raw material made us cut spear heads from places where no Magdalenian would cut into an antler, and sometimes in very curved parts that necessarily required straightening.
Reindeer antlers, Rangifer tarandus
A arcticus, B, tarandus.
Photo: Bouchud (1954)
Bâton percé engraved with a line of three horses.
13 000 BP, reindeer antler, 31 cm long.
Photo: Don Hitchcock 2014
Source: Facsimile, Musée d'Archeologie Nationale et Domaine, St-Germain-en-Laye
Conversely, whether at l'abri Fritsch, Pouligny-Saint-Pierre (Indre), in Badegoulian layers, or at La Garenne in the Magdalenian section, the notion of being economical with Reindeer antlers does not appear.
At l'abri Fritsch, Badegouliens do not hesitate to destroy a huge reindeer antler, only keeping a cortical band 3 cm wide at most.
At La Garenne, the Magdalenians were sometimes content to remove a baguette or two before throwing away a still perfectly useful antler. Sometimes, however, the antler is used so exhaustively that there remains no more than a few small pieces, on which appear, in addition to the marks where successive rods have been removed, characteristic marks of double grooving. In this case, it is likely that this is a saving, not of material, but of energy expended. The first rod requires digging two grooves, while the second, of much the same length, needs only one. It is a 50% saving in time and energy!
Spear Head straighteners
Because of many compilation publications, some images have become so common that they are gradually becoming part of our certainties. First, this representation of a hand holding an implement which is straightening an arrow shaft. This illustration of Eskimos straightening arrow shafts seems to have given prehistorians this notion that a lever is essential in straightening spear heads.
Use of an eskimo arrow shaft straightener.
Photo: Leroi-Gourhan (1943)
Also, we had thought, based on the texts published on this subject, that one straightened the spear head before hafting. However nothing proves that the spear head was hafted after being straightened, and in the case of a prior hafting, the problem of straightening is a different one.
Once the spear head has been softened by soaking, the shaft becomes a natural lever arm and leads to other solutions, in particular tying the whole length of the spear to another straight shaft while drying. The advantage of this technical solution is the ability to work on the positioning of the spear in its housing, using its flexibility, and to be almost certain to obtain, after drying, the straightness of all the components. This is essential from the standpoint of ballistics.
We also note the illustration of 'arrow shaft straighteners' published by W. Nelson in 1899, Plate XL. These are morphologically close to our bâtons percés, and it was accepted that they performed the same function. However, no one seemed worried about their differences. Eight out of twelve pieces had a hole with a squared or rhomboid section. Technically it is much more difficult to obtain a prismatic than a cylindrical hole, using the basic technique of drilling by rotation, and we do not know why the extra effort to make a prismatic hole was chosen.
The hole is always made at an angle, which is not the case with bâtons percés. We know of some examples of holes drilled at an angle, such as at Farincourt and from the Middle Magdalenian of la Madeleine, see figures, but they remain rare.
Bâtons percés with a hole made at an angle.
1 - from Farincourt
2, 3 - from La Madeleine (Magdalenian V)
Photo: Rigaud (2001)
W. Nelson has a whole plate of prismatic holes. Is it because these are the 'best pieces' as was then the custom, or is this something which definitely differentiates the two types?
Arrowshaft straighteners and point setters with prismatic holes
Photo: Nelson (1900)
Does straightening spear heads with a bâton percé leaves traces of use? Leroi-Gourhan has said nothing on this matter.
A. Peltier shows a bâton percé before and after straightening but without comment and observation of her photos provides no additional information.
One bâton percé was used by us to straighten a dozen sagaies (antler spear heads) and bears no traces of usage on the edges of the hole. However, experimental spear heads sometimes have, after straightening, transverse lines of crushing of the spongiosa that we have not noticed on the examples from La Garenne.
Macro traces of wear
The absence at present of a comparative study of the usage patterns of bâtons percés required us to do our own studies of the macro traces of visible wear under low magnification.
Two publications, among others, refer to it. Abbé Glory (1965), after describing the wear of two bâtons percés from Raymonden at Chancelade and from Saint-Sulpice de Couze, Lalinde (Dordogne), generalises as follows: 'Almost all of these bâtons percés, about 95%, show the same signs of wear, at the same locations on both examples from le musée de Périgueux.
Of the 160 pieces examined, 103 were well enough preserved to be classified without difficulty; in this group, six had only lateral or circular wear, three on one side only. The remaining 5% of disparate elements are easily explained if they were re-employed for another use.
We were able to visit the National Natural History Museum, and in the deposits made by Abbé Glory found a folder entitled 'Bâtons percés' which contains all the documents, drawings, observations and measurements gathered for the publication cited above.
The richness of these notes significantly contrasts with the brevity of the preceding paragraph, as if A. Glory had intended to publish later a more complete article. We would like to quote verbatim two paragraphs.
1. Smoothed areas and very localised depressions have a very localised shine which contrasts sharply with the patina.
2. The crest of the rim has been abraded, while the other parts have retained their sharpness.
3. Rubbing has blunted the lines of the figures engraved on the handle, including the grooves and the light embossed beads which surround the hole.
In order to comment on the zones of wear on each side of the holes of the bâtons, in a simple and eloquent way, the hole has been divided into eight sectors, starting from the 'west', with the handle pointing to the 'south', and numbering in a clockwise direction, as shown in the diagram below, Fig 6.
Fig 6.
1. Diagram by Glory defining the zones of wear at the edges of the hole.
2. Distribution of the wear noticed by Glory on 115 bâtons percés, for each sector above, by taking into account an arbitrary front and back.
3. The same wear patterns after grouping the results.
4. Total of the alternate diametrically opposed wear patterns.
Photo and text: Rigaud (2001)
We have reviewed the comments of Father Glory on 115 bâtons percés and noted the wear with the aid of several diagrams. The wear on regions 2 and 3 are no longer counted as one unit, but as two separate worn areas, zones 2 and 3. The combined results (Fig. 6, No. 2) clearly reveal four Gaussian curves with predominance of areas 2 and 3 on the one hand and 6 and 7 on the other.
The absence of objective criteria for determining the front and back prompted us to combine the two categories in the same graph (fig. 6, No. 3) where the previous trend continues. The wear zones 6 and 7 then appear much more numerous than those in Zones 2 and 3, which is perfectly normal, fractures of the end of the bâton, opposite the handle, often deprive us of data from these zones. The zones 1, 4, 5 and 8 have much less wear than the other zones, and do not seem to have been much used.
Wear is preferentially located in the axis of the shaft (zones 2 and 6, 3 and 7), but there is also wear on the sides (zones 1 and 5, 4 and 8). Finally, there is only one example for which wear affects almost all of the zones of the perforation equally.
Wear observed by Mons (1976) on the perforations of 13 bâtons percés from Placard (Charente).
Internal wear: heavy continuous lines.
Wear on the rim: dotted lines.
Drawing: Mons (1976)
Source: Rigaud (2001)
The study by Mons (1976) on 13 bâtons percés from le Placard, Vilhonneur (Charente) confirms the observations of abbé Glory (Figure 7, above). Two examples only (MAN 55128 and 55042) have a polish affecting all or substantially all of the periphery of the hole.
The wear noted has been localised, and twice was alternate.
Three broken bâtons (MAN 55040, 55099 and 55155) are particularly interesting. Wear is diametrically opposite the fractured area, possibly indicating a cause and effect relationship. By examining 56 pierced bâtons to observe non-figurative decorations, we noticed, as Abbé Glory had done, 13 pierced bâtons of various origins, where localised wear was identified.
This localised wear affected preferentially the same areas, 2, 3, 6 and 7. We have not, however, noticed identifiable polished areas with any certainty.
Two previous researchers favoured the theory of friction of a flexible solid against the walls of the hole to explain the wear patterns. On this premise, we would have expected wear that was more polished, and less rough than we have generally observed and which we are tempted to call 'flaky' or 'nibbled' in terms a craftsman might use.
Figure 8 No. 1
Bâton percé from Laugerie Basse showing traces of wear.
Photo: Rigaud (2001)
Figure 8 No. 2
Bâton percé from Laugerie Basse showing traces of 'nibbled' wear.
Photo: Rigaud (2001)
The piece MAN 48681 Mas d'Azil (Ariege), shown below, is relevant for this degradation phenomenon.
The hole is quite cylindrical and the edges remained relatively entire and undamaged before a likely short term use. The malleability of the reindeer antler, obviously very fresh at the time of use, enabled the preservation of the traces of an object inserted into the hole and manipulated, with the result of the edge being pushed up, from the inside to the outside of the hole.
Figure 9 number 1
Bâton percé SM 999-10-296 from La Garenne showing 'flaky' or 'laminated' wear in sectors 2 and 3.
Photo: Rigaud (2001)
Figure 9 number 2
Bâton percé from Mas-d Azil, MAN 48681, with the edge of the hole pushed out.
Photo: Rigaud (2001)
Reindeer antler is organised much like wood, in layers, and there is no doubt that, if the action causing the fracture had continued, the edge would have gradually disintegrated resulting in the formation of the 'nibbled' wear discussed above.
In this case, it is impossible that the wear was caused by straightening a spear head, an action that would have led inevitably to the crushing of the edge of the outside of the hole towards the inside of the hole.
In any case, these traces can not be the result of the passage of a very rough and very hard object, and their appearance following the passage of a flexible and rough object remains entirely possible, but under high pressure.
This 'nibbled' wear often affects diametrically opposed areas, and it is as if the action causing the wear was produced from the centre of the hole to the outside.
Other Hypotheses commonly put forward
We have never used a pierced bâton as a spear thrower. The demonstration by Abbé Glory, developed from experimental pieces in wood was very well conducted and results in wear occurring at the same place on the palaeolithic examples. This demonstration, however, was not conclusive.
First, any thong, belt, rope, twine or braid moving inside the hole in the longitudinal direction inevitably produce wear in the same places, even if the purpose of the action is totally different.
On the other hand, it is not able to produce the 'nibbled' wear directed from the inside to the outside in the direction away from the shaft, that is to say on sectors 2 and 3 preferentially.
As for the last hypothesis to date, that of the handle for a fire drill, we have not tried that either. This ignition process seems complicated compared with ethnographic techniques commonly used.
This technique, involving rotary friction of reindeer antler against wood must leave traces of wear or more likely polishing over the entire inner periphery of the hole that the current evidence has not confirmed.
First approach to the enigmatic decorations
Leroi-Gourhan, Abbé Glory, P. Noiret and A. Peltier devoted several studies to the decorations on pierced sticks, although that of Abbé Glory has never been published. Their respective accounts of figurative or naturalistic decorations schematically show some similarities regarding the presence or absence of decorations but raise further questions, see Table I below:
Author | Number of bâtons studied | Number of categorised decorations | |||||||||||
---|---|---|---|---|---|---|---|---|---|---|---|---|---|
Studied | Entire | Incomplete | Undecorated | Decorated | Fish | Horse | Cervids (deer, reindeer, elk, moose) |
Bovids (aurochs, bison) |
Birds | Man | Phallus | Geometric | |
A. Leroi-Gourhan | 81 | 13 | 12 | 7 | 5 | 2 | 13 | 11 | |||||
Abbé Glory (1) | 331 | 54 | 150 | 20 | 32 | 16 | 7 | 8 | 4 | 4 | 54 | ||
P. Noiret (2) | 361 | 86 | 275 | 32 (2) | 329 | 36 | 55 | 42 | 25 | 28 | 21 | 34 | 175 |
A. Peltier | 107 | 46 | 71 | 34 | 73 | 3 | 15 | 2 | 4 | 1 | 4 | 6 | 67 |
Comparison of records by Leroi-Gourhan, Glory, Noiret, and Peltier
(1) Glory data from the Muséum National d'Histoire Naturelle. (2) Objects assigned by A. Rigaud from those denoted by P. Noiret as 'undecorated' or 'no ornamentation'.
Source: Don Hitchcock after Rigaud (2001)
Where is the beginning and end of the concept of decoration? (91% decorated according to P. Noiret, 45% according to Abbé Glory). What schematic motifs are actually fish, birds, humans, and phallus, to arrive at such differences?
Regarding geometric patterns, A. Leroi Gourhan has only one category, Abbé Glory selects eleven, while P. Noiret identifies forty-three different categories. On this subject, the analyses of one and the other vary significantly. This is what has led us to group under the heading of enigmatic the purely geometric designs, the phallus, the tails of fish and bird beaks.
La Garenne may well be a privileged site, an observatory for us of Magdalenian customs, it does not however have harpoons and has few of the beautiful decorations so common elsewhere.
Décor et fonction (Decoration and function) by Allain et Rigaud (1986) brought a new perspective on how to view isolated decorations but this work could never have occurred without the ideas of J. Allain on the genesis of the Magdalenian harpoon, discussed for the first time in 1957, in Allain et Descout (1957).
We briefly summarise this work on the genesis of the Magdalenian harpoon:
• We now have enough examples of bladelets associated with spears to ask whether reindeer antler harpoons were not copies of composite harpoons.
• In the decoration of the shafts of harpoons, the carved motifs evoke a hypothetical composite archetype, with the presence of ligatures for holding together two baguettes, two sides between which the barbs find themselves caught.
• The barbs seem to be organised roughly into two types: angular barbs evoking a lithic origin, and hooked barbs evoking the claws or teeth of an animal.
Experimentation with fox canines leads to a staggered organisation of the housing intended to accommodate the roots of the teeth to avoid weakening the wooden shaft as shown in figure 10 below.
Figure 10
If harpoons had been constructed originally using fox teeth, the staggered arrangement shown here reduces the width of the shaft by half.
Photo and text: Rigaud (2001)
Amongst the harpoons shown in Julien (1982), 203 harpoons with two rows of barbs have an alternating arrangement of teeth as compared to only 40 where they are directly opposite.
If we accept this hypothesis as a general one, we should find on other tools not just these indispensable complements of knives in all civilisations of nomads or farmers, but also the remainders of simpler techniques or reminders of habitual actions.
Figure 11a
In 1986, it was in this spirit that we looked at the central decoration of a pierced bâton from Laugerie-Basse, and believed we could discern a copy of a ligature or whipping, as shown at left.
Photo and text: Rigaud (2001)
Fourteen years later, the careful observation of this piece left us speechless with admiration as the decoration is full of technological realism.
Compared by White (1986) to threads on a screw, eleven to twelve contiguous turns in relief seem to grip the handle. Abbé Glory had written in his notes:
'... handle decorated with a spiral winding of eleven turns giving the impression of a rope or strap, whose end was concealed in the winding' (Glory collection, MNHN, Muséum National d'Histoire Naturelle).
Figure 11b
On the sides, never shown in published drawings, the turns have been removed by a conscientious scraping, but a slight regularity detectable under the finger and when illuminated by an oblique light source proves that originally it was indeed a continuous spiral. Intentionally or not, only the three closest turns of the proximal part have not been scraped.
Photo and text: Rigaud (2001)
On face A in the drawing Figure 11b above, the lower coil seems to disappear under the contiguous turns, and on the side D, a small piece appears to come out of the coil, reinforcing the impression of a faithful copy.
On sides A and C, two longitudinal recessed strips overlie the turns, with the exception of two or three. The execution of these removals is clearly less carefully done than the rest of the decoration and it was necessary to draw the different phases of the completion of a ligature to try to interpret them as shown in Figure 12 below.
Figure 12
On side A, having tucked the end of the string under the first two turns (1), a loop is laid on the completed turns as shown. The sides of the loop gradually disappear under the coils (3) and, when the number of turns is sufficient, the end of the string is inserted into the part of the loop still showing above the coils (4).
Pulling on both strands of the loop (5) the end of the string can then be dragged under the turns, the excess line is pulled under the whipping, appearing, if it is long enough, at the second coil as shown in the diagram, and the loop is pulled out.
The now invisible, and securely held ends are shown by dotted lines. One may wonder therefore, whether the engraver could not, by making some of the lines deliberately fuzzy, indicate the beginning and end of the ligature, overlain by the winding.
Photo and text: Rigaud (2001)
( note that for clarity, the end of the string tucked under the first two turns is not shown in (2) above, but reappears in (3) - Don )
Other decorations representing ligatures or coils support this first observation, particularly that of the pierced bâton from Gourdan (Haute-Garonne), MAN 47049 (fig. 13, No. 1, at left, original at right).
The same little detail imitating the beginning of a ligature transforms, at one stroke, rods, flutes and other pieces with parallel sides such as, in the Gourdan bâton percé shown at left, the parallel incisions in an entirely characteristic assembly, slightly angled, with good even turns, wound in the opposite direction of the specimen from Laugerie Basse.
In fact, there is a succession of rings and not an actual spiral, but the overall impression is equally successful.
In the two cases shown here (Figure 13, left) and above (Figure 11a), the ligature decoration is in the middle of the shaft.
Photo (left) and text: Rigaud (2001)
Photo (right): Don Hitchcock 2015
Source: Salle Piette
Figure 13, No. 3
On the bâton percé decorated with a salmon from Enlène (Ariege), the same pattern, but with significantly less relief, occupies the proximal part of the shaft.
Photo and text: Rigaud (2001)
The original bâton percé decorated with a salmon from Enlène (Ariege).
Photo: http://www.volvestre-patrimoine.info/
Figure 13, No. 5
There is also, in the National Antiquities Museum an extraordinary piece of ivory (MAN 47060) from Mas d'Azil which is generally regarded as a pendant because of two holes in the piece. Unfortunately, we were not allowed to examine it, for conservation reasons.
The layers in which this object was found have been dated to 13 000 BP.
Photo and text: Rigaud (2001)
Phallus in carved ivory from Mas d'Azil, discovered by Édouard Piette.
Length 95 mm, Diameter 17 mm
This piece has two holes, leading observers to believe that it is a pendant.
At the proximal end shown at right
are eight contiguous lines of cords shown in relief denoting the 'whipping' denoted by carving. Like the harpoon from Kniegrotte, Dobritz (Germany), shown below, it seems that the attention to detail was extended to include the strands of the cord.
Cat 359, MAN : 47042 (APM10503)
Photo (left): © photo - Loïc Hamon, Musée des Antiquités nationales, Saint-Germain-en-Laye.
Photo Source: http://www.culture.gouv.fr/culture/app/eng/96ce1735.htm
Photo (right):
http://www.culture.gouv.fr/public/mistral/joconde_fr?ACTION=CHERCHER&FIELD_98=REF&VALUE_98=50010008046
At the distal phalliform end, a third, broken perforation could be the remains of the hole of a bâton percé.
Photo:
http://www.culture.gouv.fr/public/mistral/joconde_fr?ACTION=CHERCHER&FIELD_98=REF&VALUE_98=50010008046
Figure 13, No 6
We find the same thing, the use of a bâton percé as a pendant, at La Garenne for a miniature bâton percé, the use of which is not clear, but it has a hole for suspension as a pendant.
Photo and text: Rigaud (2001)
Harpoon head from from Kniegrotte, Dobritz showing detailed cord design.
Photo: Braun (2009)
Figure 13 No. 4
Abbé Glory (archive MNHN) also notes, concerning this example from La Madeleine, 60338 MAN: 'Both sides are decorated with bovine heads and on the edge of the sides is a string design, one side with two strings, the other with three strings.'
Photo (left) and text:
Rigaud (2001)
Photo (right): Don Hitchcock 2014
Source: Original, Le Musée National de Préhistoire, Les Eyzies-de-Tayac
Figure 13 No. 2
Finally, this example from Laugerie Haute, unfortunately too degraded to see the beginning of the winding, carries perhaps some turns around the entire shaft. We also noticed looser overlapping spirals in the manner of representations of links, with or without figured strands observed also in an example from Isturitz (fig. 14, No. 1) or another from Kesslerloch, Thayngen (Switzerland) (fig. 14, No. 4).
Photo and text: Rigaud (2001)
We also noticed looser spirals overlapping in the manner of representations of cords, with or without figured strands, observed in the Isturitz example (fig. 14, No. 1, below) and an example from Kesslerloch, Thayngen (Switzerland) (fig. 14, No. 4 below).
Figure 14 Nos. 1, 2
Engravings showing crossed cord bindings, (left to right) Isturitiz and la Madeleine.
Photo and text: Rigaud (2001)
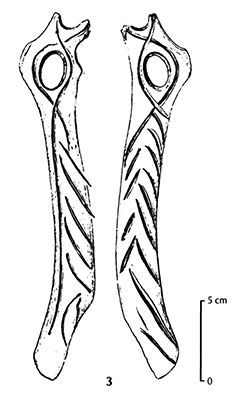
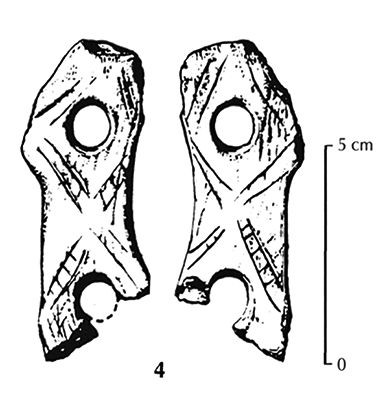
Figure 14 Nos. 3, 4
Engravings showing crossed cord bindings, (left to right) Laugerie Basse, Kesslerloch.
Photo and text: Rigaud (2001)
Figure 14 No. 5
Engraving showing crossed cord bindings from Laugerie Basse.
Photo and text: Rigaud (2001)
Plagiarising the theoretical model of the composite harpoon designed by Allain, we imagined a wood / bone assembly using cord:
Figure 15
A thoracic vertebra form a deer whose medullary canal diameter was about 15 mm was used as the basis for this first test
This reconstruction of a hypothetical tool is certainly able to be made with only the tools available in the upper Palaeolithic.
First, it uses reindeer antler split lengthwise using flint tools to act as a housing for the vertebra. After shaping the ends of all three parts, the oblique surfaces resulting are scratched to promote the adhesion of the glue and the whipping cord which makes the three parts into one solid whole.
( note that there are two distinct methods for the cord used to tie the whole construction together in use here. In the first, the cord starts and ends at the bottom of the double shaft, and in the second it starts and ends at the top of the shaft, just below the vertebra. Note also that a skilled artisan would have no difficulty in combining the two, with a band of whipping at both the bottom and the top of the double half shafts should that arrangement offer significant advantages - Don )
Photo and text:
Rigaud (2001)
Finally, after glueing, a cord is 'whipped' around the shaft at the join in order to complete the joint and strengthen it.
It is possible to wrap the line around the joint, and organise the turns of the cord so that the object is constructed as shown in the diagram. (Figure 15 No. 1 above)
What we wished to have was:
1 seven turns of cord locking the end construction in place.
2 large coils of cord encircling both half shafts.
3 lashing down the left transverse process;
4 the body of the vertebra left untouched;
5 lashing down the right transverse process;
6 the turns crossing neatly at the midline front and back ;
7 finishing off the whipping in the normal manner with the end of the cord hidden and secured under the other turns.
Reducing the lines carved on bâtons to the minimum, we find, at the front,
• crosswise bars of the ligature;
• crossing windings noticed among other bâtons for example on the bâton from Isturitz;
• around the hole, particularly common; an outline:
• chevrons, also frequent.
In this assembly, the medullary canal has approximately the same inclination as the hole of the 'arrowshaft straighteners'.
Using this scheme, the method might seem attractive, but mechanically, it would be better to perform a ligature with contiguous turns at the spinous process wedged between the two half rods, like spear bases (fig. 15 , No. 2). But we know of no example of a decoration that depicts this second type of assembly.
Figure 13 No. 2
As for tying contiguous turns along the whole shaft as in the Laugerie Haute example shown here, it would take a very long cord. Obviously, such an instrument might well straighten spear points or launch projectiles or do anything else.
Photo and text:
Rigaud (2001)
The torteiraes or rope twisters hypothesis
For nearly fourteen years, and over many publications, discussing many different styles of cord decoration, we were encouraged to seek a relationship between cords and bâtons percés and, of course, bâtons percés used in the manner of the portuguese torteiraes to make rope, which seemed worthy of a comparative experiment. History of the hypothesis
This hypothesis usually attributed to Breuil (1954) is in fact the result of correspondence with Ruy d'Andrade who had noticed a morphological resemblance between the two objects and mentioned it to l'abbé Glory. Together with a photo of the design and a drawing by Breuil the result is self-explanatory (fig. 16, No. 2).
The torteiral or torneiral or rope twister (Fig. 16, No. 1) is a wooden stick ca 35 cm long, pierced at one end with a hole into which is threaded a wooden stick with a bulge at one end.
Fig 16 one and two.
Fig. 16-2, fixation du fil à caret sur le torteiral ; 2, filage de crin de cheval avec un torteiral ; 3, chantier de fabrication de câbles.
1, 2, dessins A. Glory ; 3, dessin extrait de La Grande Encyclopédie, p. 642.
Photo and text:
Rigaud (2001)
The drawing accompanying the article (fig. 16, No. 2) includes an error: the twisted yarn can not drag the ground, but must be wound on the handle of torteiral to avoid an automatic twist. Moreover, in the photo accompanying the article, the thread seems to fill the handle of the moving object.
In addition, it is actually possible to just fold in half the two single strands of twisted yarn to make a two-strand rope but it generally gives poor results, the turns becoming less tight as we approach the end.
The Lascaux rope with three strands of plant fibre could therefore not be made using this technique (Delluc et Delluc, 1979).
Fig 16 number three.
Note that in this diagram of a more modern method, a two ply rope is being made.
This appears to be a specialised tool for plying together an S and a Z twisted yarn into one. The cranks on the right are joined by a cog. Turning the crank on one of the hooks would turn the other hook in the opposite direction because of the cog connection. It is now more normal to ply two yarns with the same twist, that is, two S twist yarns are twisted together in the Z direction, or two Z twist yarns are plied in the S direction.
Note also that in this arrangement, the actual twisting of the cords into rope is not done by the tension of the cords themselves, but by turning the crank M.
There is, however, a 'rope maker's top' shown, and the larger close up appears to be being used to make a three ply rope, though it is unclear what the extra cord at E is for. The rod F through the rope maker's top is for an operator to control the movement of the top and its effect on the rope so that a symmetrical rope is created as the top is moved towards the hooks at M.
The wheels at R on the sledge are to take care of the decrease in length of the rope as it is made from the longer cords, the decrease being of the order of one sixth.
The reason for including this diagram, and my explanation of it, is that the diagram is part of the paper being translated.
Text: Don Hitchcock
Photo:
Rigaud (2001)
Source for the image: La Grande Encyclopédie, p. 642
Twisting rope at a medieval fair, the Medieval Market in Turku, Finland.
Unfortunately the rope maker's top is hidden by the workers.
Photo: Samuli Lintula
Source: Wikipedia
Permission: cc-by-2.0, cc-by-2.5, licensed under the Creative Commons Attribution 2.5 Generic licence
Here we can see a wooden cross shape being used as a rope maker's top.
It is easy to see that a bâton with three or four holes could be used just as this is being used, in this case to make a four ply rope by plying the 's' spun (clockwise) cords in the 'z' (counterclockwise) direction.
Photo: © Christina Coutts
Souorce: http://www.work4idlehands.com/archives/2007/09/
From the abstract to Kilgore et Gonthier (2014):
Certain types of Paleolithic perforated bâtons possess the characteristics of a type of composite tool,a spinning device, used to fabricate cords of different diameters. These devices are composed of a rotor (the perforated bâton) made of antler and a stator or crank-shaft made of wood, examples of which have not yet been found. The bâtons’ knob-like projections can be seen as the point of attachment by which horse hair is twisted into strings and then laid up into larger-diameter cordage.
C. Kilgore examining a perforated bâton from Laugerie-Basse, LesEyzies-de-Tayac, Dordogne, France. Coll. de Vibraye, 38.189.1264. MH/MNHN.
( this appears to be a facsimile, an impression heightened by the fact that the researcher is not wearing gloves while handling it - Don )
Photo: E. Gonthier, 2012.
Source:
Kilgore et Gonthier (2014)
Use as an aid to making rope.
Laying up or twisting together of the 3 plies into a single rope. One end remains stationary, while the other end turns. The Paleolithic bâton with its forked knob guides the 3 plies as they twist together into a single rope of the hawser type.
Drawing: E.Gonthier.
Photo:
Kilgore et Gonthier (2014)
An assistant provides help to turn the stick in a circular motion by rotating the torteiral thus twisting the horse hair while the spinner feeds the fibre into the yarn by drawing on the reserve fibre, carded in advance. The yarn lengthens gradually, forcing the assistant to move back in order to keep tension on the yarn until it finally reaches the required length.
The torteiral therefore plays both the role of a wheel, since the turning motion is continuous, and that of a spindle, since it allows the yarn produced to be wound onto the shaft.
Techniques of modern rope makers
Going through the literature of the rope makers, and by studying closely the survivals in Berry, the historic French province, of artisanal rope, we realised that a number of errors were made in these interpretations.
In his new complete manual of cord making, Laurent (1911) provides us with valuable information:
The yarn is spun, which means that one can then make the rope by plying together several single yarns to create the rope.Thus if a rope of two, three or four strands is required, it is sufficient to use a single rope maker's top having two, three or four grooves.
To make a two ply rope, the rope maker attaches two spun cords at one end to hooks, and the other to two hooks (or to a locked swivel), onto which the two cords are tied. The hooks are then turned so that the two cords are very tightly twisted. Two (or three, for three ply rope) of the ends are brought together and tied to a swivel, or the swivel is unlocked, at which point the cords will automatically twist together unless kept apart.
note that in order to make a two or three ply rope, the cords must twist together in the opposite way to that in which they have been spun - Don )
To control the plying process, a piece of shaped wood known as a 'rope maker's top' is placed between the strands, keeping them apart on one side, but allowing them to twist together behind it as it is moved forward, forming a rope behind the shaped wood. In this case the plying is automatic because of the tight twist of the strands.
![]()
Rope maker's top.
Photo: https://www.youtube.com/watch?v=By8K5mKSwDA
When this is completed, the final rope will be found to be about 85% of the original length of the yarns used, as a result of the plying process, and the rope does not unravel.
Sometimes the swivel is replaced by a handle that is rotated in the opposite direction of the wheel at the time of the plying.
There is also therefore no rope having just one strand, since it would tend to untwist, as well as twisting on itself naturally from the elastic force that it has acquired. It is from such observations that true plied yarns originated.
Although homemade ropes are still made in Berry, they are almost entirely folk art made during demonstrations of popular traditions. A small number of farmers and graziers, however, continue to make ropes for their animals in this way.
If the rope making devices were to decay, they can be easily repaired or replaced. The devices include the three essential components described by Laurent (1911):
A spinning wheel consists of:
• four boxwood hooks turning simultaneously
• a crank handle attached to a sled, which also has boxwood hooks to which are attached four strands
• a cross cleverly replacing the rope maker's top. For a long time hemp fibre has not been used, it was then replaced by baling twine. Formerly this was made of sisal, it is currently composed of synthetic fibres.
Three people are required to make a rope: one activates the spinning wheel, the other winds the handle at the tailpiece, while the third moves the cross/rope maker's top while calling for the ensemble to turn faster or slower, with the sledge being moved as necessary.
After attaching all the cords from the spinning wheel to the crank, twisting of the fibres starts until the person at the tailpiece judges, by experience, that sufficient torsion has been acquired in the yarn. He begins to move the cross after ordering the other crank to be rotated smoothly.
As the rope is twisted together, the tension becomes greater and the sled moves to shorten the length between one end of the rope and the other to avoid breakage of any part of the mechanism. Nylon ropes thus made can lift 300 kg to 400 kg, the sisal rope a little less.
Rope making tool at Hohle Fels in situ, as first discovered in August 2015.
Photo credit: © University of Tübingen
Source: http://www.heritagedaily.com/2016/07/researchers-discover-how-rope-was-made-40000-years-ago/112211
( The rope making tool above, shown in the image at left after cleaning and restoration. It is apparently an analogue of what is now known as a 'rope maker's top', see above. This one has four holes, of which three are the same size, while a fourth is smaller than, and more distant from, the others.
If the four holes were used, it would allow the plying of four strands of cord to make a strong rope.It is no accident that there is a strong 'handle' on this tool, necessary for the making of rope while using it as a rope makers top. A strong and steady hand and arm is required during this operation.
It should be noticed also that the three larger holes have distinct spiral incisions, while there is a hint of spiral incisions in one view of the fourth hole. Of the larger holes, three spirals are in a clockwise direction on one side of the tool, on the left image as shown here, but when we examine the other side of the tool, the lower hole, the one closest to the handle, has an anti-clockwise spiral.
This is extremely puzzling. One would expect the other two to also have an anti-clockwise spiral, as can be confirmed by the reader if they poke a pencil through a piece of paper, and rotate it clockwise. From the other side, the pencil will appear to rotate in an anticlockwise direction.
If we look at the fourth, smaller hole, there are traces on one side of a clockwise set of spiral incisions, with a possible anticlockwise set on the other side.
Some background for those unfamiliar with spinning and plying yarn: when one spins woollen yarn on a spinning wheel, it must then be plied, and typically home spinners and weavers use two ply for knitting projects.
The yarn from two spools of yarn is plied on the spinning wheel, but in the opposite direction - if the two yarns were spun in the clockwise direction, the plied yarn is obtained by spinning in the anticlockwise direction, or to use the jargon, 's' spun yarns are plied in the 'z' direction and vice versa, usually by starting the spinning wheel spinning in the opposite direction to the normal.
The user uses the fingers of one hand to keep the two yarns apart while they are being plied, and this gives a strong and even plied yarn.
However, if rope is to be spun, it is normal to spin the single ply 'yarns' all the same way, and to ply either three or four such yarns in the opposite direction.
Because of the inherent coarseness and roughness of typical rope, it is normal not to use the fingers of the hand as is done for plying wool for knitting, but to use what is called a 'rope maker's top', as shown in the photograph above.
This consists of a piece of wood in the shape of an elongated half ellipsoid, with four grooves down its side to receive the four yarns being plied together, as shown in the attachment and below in this email.
Only by using such a device can a strong and evenly plied rope be made. The requirements for strong rope are a strong fibre, tightly spun yarn, and a tightly and evenly plied final result.
I believe that the four holed tool discovered at Hohle Fels is an analogue of the four grooved 'rope makers top' and is used in the same way.
That is, the four yarns are introduced to the four holes in the tool, tied together at one end, then a crank or similar is turned, in the opposite sense to the ply of the original four yarns, and the tool is gradually moved back, so that the yarns are plied together in an orderly, even way, giving the maximum strength to the rope.
A rope made using this technique would be very much stronger, and much more pliable, and indeed much thinner than the huge 'cable' that the researchers made in the photo I found of them using the four holed tool to spin a one ply yarn. A one ply yarn is not nearly as useful as a plied yarn. Even two ply is far, far better than a one ply yarn. - Don )
From the source:
'Prof. Nicholas Conard and members of his team, present the discovery of a tool used to make rope in today‘s edition of the journal: Archäologische Ausgrabungen Baden-Württemberg.
Rope and twine are critical components in the technology of mobile hunters and gatherers. In exceptional cases impressions of string have been found in fired clay and on rare occasions string was depicted in the contexts of Ice Age art, but on the whole almost nothing is known about string, rope and textiles form the Paleolithic.
A key discovery by Conard’s team in Hohle Fels Cave in southwestern Germany and experimental research and testing by Dr. Veerle Rots and her team form the University of Liège is rewriting the history of rope.
The find is a carefully carved and beautifully preserved piece of mammoth ivory 20.4 cm in length with four holes between 7 and 9 mm in diameter. Each of the holes is lined with deep, and precisely cut spiral incisions. The new find demonstrates that these elaborate carvings are technological features of rope-making equipment rather than just decoration.
Similar finds in the past have usually been interpreted as shaft-straighteners, decorated artworks or even musical instruments. Thanks to the exceptional preservation of the find and rigorous testing by the team in Liège, the researchers have demonstrated that the tool was used for making rope out of plant fibers available near Hohle Fels. 'This tool answers the question of how rope was made in the Paleolithic”, says Veerle Rots, “a question that has puzzled scientists for decades.'
Excavators found the rope-making tool in archaeological horizon Va near the base of the Aurignacian deposits of the site. Like the famous female figurines and the flutes recovered from the Hohle Fels, the rope-making tool dates to about 40,000 years ago, the time when modern humans arrived in Europe. The discovery underlines the importance of fiber technology and the importance of rope and string for mobile hunters and gatherers trying to cope with challenges of life in the Ice Age.
Prof. Conard’s team has excavated at Hohle Fels over each of the last 20 years, and it is this long-term commitment that has over and over again paid off, to make Hohle Fels one of the best known Paleolithic sites worldwide.'
Photo credit: © University of Tübingen
Source and text: http://www.heritagedaily.com/2016/07/researchers-discover-how-rope-was-made-40000-years-ago/112211
Close up of the holes.
Photo credit: © University of Tübingen
Source: http://www.thehistoryblog.com/archives/date/2016/07/24
Close up of one of the holes, showing the carefully cut spirals
Photo credit: © University of Tübingen
Source: http://sciencebulletin.org/archives/3576.html
Close up of a hole in a bâton percé from Solutré, showing similar carefully cut spirals to those found in the object from Hohle Fels. The spiral shown here is turning clockwise.
Photos (in order, L to R): http://www.hominides.com/html/dossiers/baton-perce.php, http://www.hominides.com/html/lieux/musee-prehistoire-solutre.php, http://www.balades-bourgogne.fr/fr/musees-art-histoire/musee-departemental-de-prehistoire
Source: Musée de Solutré-Pouilly
The bâton percé above, showing both sides of the hole. There are no spirals on the other side.
Age: ca 19 000 - 12 000 BP, Magdalenian.
Discovered at Solutré in 1866 by Arcelin.
Material: bone.
Length 118 mm, width 50 mm.
Photo: © Pierre Plattier
Source: http://www.culture.gouv.fr/Wave/image/joconde/0601/m017283_0010785_p.jpg
Text: Adapted from http://www.culture.gouv.fr/public/mistral/joconde
This multiperforated bâton percé above is from the final Magdalenian of Aizkoltxo cave (Mendaro, Gipuzkoa, Northern Spain), circa 15 000 BP.
The Aizkoltxo cave is located next to the bank of the Deba River, close to other caves with Upper-Final Magdalenian occupations (Agarre, Ermittia, Praileaitz I and Urtiaga). As a result of poaching activity, it was decided to carry out a survey to evaluate the stratigraphy of the site and contextualise the recovered remains.
In the course of these works, a level attributable to the Upper-Final Magdalenian was identified, whose formation process is unusual. In it, in addition to an abundant lithic and bone industry dating from 14 864 - 14 160 cal BP, the baton that we describe was located, which preserves at least four perforations and is profusely decorated with figurative motifs (a deer in frontal view, and two antlers of deer in addition to a horse and a mountain hare and signs (simple lines, tapered, Vs embedded, Vs parallel, etc.).
This exceptional object, together with others, corroborates the close relationship of the deposits of the Cantabrian Coast with those of the Bay of Biscay and the Western and Central Pyrenees.
( note that the three holes on the left of this sketch would have served a useful purpose if employed as an aid to plying yarn - Don )
Text above: adapted from Ochoa et al, (2020)
Photo: © Universitat Politècnica de València
My thanks to Miguel Obeso for drawing my attention to this important piece, perhaps the only bâton percé extant from the Iberian Peninsula.
Experimental use of bâtons percés as Torteiraes
It seemed worthwhile to consider making rope from bâtons percés used as torteiraes, or rope twisters. The first problem encountered was the attachment of the cord to the bâton, consisting of particularly smooth antler material, which made the operation difficult. With a bâton percé facsimile in wood, fixing at a single point, described by Ruy d'Andrade in his correspondence with H. Breuil, has the great disadvantage of making storage on the shaft difficult and thus limits the length of the rope to about six metres.
Even when one manages to wrap the cord on the rod, you cannot continue spinning using the attachment shown in figure 16 number 1 (above) because the spun yarn often twists around the stick, making progress difficult.
Figure 17
Experimental bâtons percés made of wood, except numbers 2 and 5, which are of reindeer antler.
Numbers 2, 4, 5 and 6 were used as torteiraes.
Drawings: A Rigaud
Source and text: Rigaud (2001)
We opted for a double attachment of the cord to the bâton: one to the shaft, another to the lateral branch, which shifted the yarn to one side relative to the axis of rotation. (Figure 17, No. 2)
Over time, four systems enabling knotless attachment/quick release of the cord emerged:
• as with the torteiraes, a circular groove used on broomstick handles of old is a technically quick solution in terms of attachment by simple methods. (Figure 17, No. 2.)
• a bulge divided by two cuts avoids the sliding of the string. The original bulge must be large enough to accommodate the amount of material to be removed. (Figure 17, No. 6)
• a beak style notch large enough to achieve, with care, a foolproof attachment. (Figure 17 Nos. 4, 6, in the diagram above)
• A ligation or whipped cord with sufficient length of the cord to make it possible to wind the yarn on it securely to serve the same purpose as a bulge. (Figure 17, No. 4)
Such a locking system on smooth surfaces such as poles or ropes is still used today in circuses to attach the ropes supporting the marquee, or in rock climbing, under the name 'Machard ( Klemheist ) knot.'
Figure 43
'Phallic' attachment systems: 1, La Madeleine; 2, Isturitz; 3, Farincourt; 4, Isturitz; 5, Le Mas-d'Azil; 6, Arudy; 7, La Madeleine;
8, Le Roc de Marcamps; 9 and 10, La Garenne.
It is of course possible to combine the first two systems with the third to obtain an engraved phallus with one or more 'penis heads' (Figure 43, No. 4, at left, from Isturitz) which, anatomically, is at the very least curious, but practical to attach yarn or cord to.
Drawings: A Rigaud
Source and text: Rigaud (2001)
Figure 42
Possible systems that prevent the rope from slipping on the shaft: 1, La Garenne; 2, La Madeleine; 3, La Garenne;
4, Le Mas d'Azil; 5, Les Combarelles II; 6, Laugerie Basse.
These examples were replicated on some bâtons percés, and other possible solutions are likely, such as the spiral of the bâton percé of Laugerie Basse (fig. 42, No. 6, at left).
We needed seven people to ply a rope with four strands:
• a spinner
• four 'Tortilleurs' operating the pierced sticks
• one turning the 'crank'
• one moving the rope maker's top as required.
Drawings: A Rigaud
Source and text: Rigaud (2001)
This is the original of the drawing at Figure 42 No. 4 above, from le Mas d'Azil, showing the opposite side.
This may show the eventual system developed to stop a cord sliding off the shaft of the bâton percé.
( note that this piece has also been described as a musical instrument, a scraper, or scraped idiophone, by the curators at le Musée d'Archeologie Nationale et Domaine, St-Germain-en-Laye, and to have been made from a salvaged broken bâton percé - Don )
Photo: Don Hitchcock 2015
Source: Original, Musée d'Archeologie Nationale et Domaine, St-Germain-en-Laye
Text: Rigaud (2001)
In the absence of hemp fibre and not having enough horsehair, we opted for a mix of horse hair and bison wool, the length of the first to compensate for the shortness of the other. The Vikings would have used a mixture of horse hair and linden fibre (in our opinion lime bark fibre). (Vesilind, 2000)
Nettle fibres may be another solution. This plant, less durable than hemp, has a fibre which is nevertheless quite strong, and is used commercially in tissues, and in the mix of fibres in banknotes. Formerly cultivated in Sweden, nettle is cold hardy, and pollen from other members of the nettle family Urticaceae may be found in ancient deposits from La Garenne, as noted by Leroi-Gourhan in Allain et al (1985).
We do not know, however, whether this is the variety Urtica dioica traditionally used as a textile fibre. This variety is not sensitive to cold, and once replaced hemp and flax in the Kamchatka Peninsula in the far north of the Pacific.
The structure used for making the cord consisted of a tripod 250 cm high, composed of three forked branches connected by a rope binding, in the manner of tent frames. A crossbar was fixed to two posts, with a hole of 15 mm diameter to allow the passage of the four yarns which were to be plied together, knotted at the end and with a single stick replacing the crank.
We chose to use four different experimental bâtons percés:
• one of reindeer antler with two circular incisions defining two 'acorns' (Figure 17, No. 2);
• one of beech with a bulge at the proximal end and a 'beak' on one side branch (Figure 17, No. 6);
• one of boxwood with a kind of button;
• a composite - using a deer vertebra / split shaft antler combination, the two split antler shafts were glued and whipped in order to hold the deer vertebra securely. ( see Figure 15 )
The various yarn fastening systems at the beginning of the process, and the storage upon completion of the yarn, demonstrated the origins of some of the graphical decorations.
After having carded a horsehair/wool blend, a spinner mastered the technique of spinning, and, assisted by a 'tortilleur', made four pieces of yarn to 6 to 8 metres long. If the length exceeds 8 metres, it is necessary to wind the yarn produced on the shaft, used as a spindle. Below 8 metres in length this is not necessary, so long as it is held by a 'tortilleur' to avoid premature automatic twisting.
When stored on the shaft, the shapes taken by the thread can explain the decorations of windings, crossed or not crossed, the chevrons or v shapes, the spindles and notches and opposed cupules in pairs on an angle that may prevent the yarn from slipping off. The only problem encountered during the making of the rope was the breaking of one of the four yarns when it was twisted too tight. Moreover, the four yarns were of different length and uneven twists, and thus the regularity of the rope was not perfect.
With a diameter of about 8 mm, it withstood a tension of 80 kg. As we mentioned above concerning the hypothesis of its use as a fire drill, it quickly produces a shiny circular buffing over the entire periphery of the hole, which excludes this type of use for reindeer antler bâtons percés. However, the resemblance between the graphics and the patterns made by winding the yarn on the shaft, the necessary adjustments to attach the yarn to the bâtons percés, and the certainty that cords did exist in the Upper Paleolithic, are altogether quite intriguing.
A second approach to the enigmatic decorations
In various scientific studies of the bâtons percés, the authors seem to focus on concerns of their own, and do not examine this phenomenon. Thus, we will ignore the designs using animals on which so much has been written, and secondly, we will not take into account the different types of bâtons percés defined by A. Peltier, except for bâtons percés with more perforations whose identification for use is unambiguous.
Indeed, the first three categories are based on the morphology of the head and does not reflect any technological or mechanical difference. After analysing sets of bâtons percés, the authors are able to pose the question of the possible relationship between décor and presumed function.
Breuil (1954) considered the torteiraes hypothesis as one of the most efficient uses, and saw a direct relationship between this function and some decorations: 'spirals imitating a rope; engravings in relief or engraved; bulges or transverse parallel grooves on the shafts of the bâtons percés; derived decorations.'
With J. Allain Allain et Rigaud (1986), we wrote that some decorations (cupules and notches) may be facilities for a better grip and the phallic representations are symbolic decorations in connection with the straightening of spear heads.
A. Glory (Glory archives, MNHN) wrote that 'there is no necessary relationship between the decoration and the manuals envisaged'. Noiret (1990) concludes that 'the nature and meaning of the relationship between the staff and the decor are not accessible to us.' For the latter two authors, it is never a question of usefulness, but always one of decoration.
Figure 18
Signs and morphologies possibly inherent in the manufacture of ropes with bâtons percés:
A - signs related to the windings
B - signs related to attachment problems on a naturally slippery material
C - signs related to winding problems (arrangements avoiding the sliding of the yarn on the shaft).
Drawings: A Rigaud
Source and text: Rigaud (2001)
Figure 19
Summary of decorations based on the signs/symbols used in Figure 18.
Monotrou - one hole in the bâton percé.
Multitrou - two or more holes in the bâton percé.
Décors des têtes - decorations on the head of the bâton percé.
Décors des fûts - decorations on the shaft of the bâton percé.
Photo and text: Rigaud (2001)
Despite the numerical differences, the bâtons completely deprived of decorations and the others, with decorations so minimalist that you can hardly call them changed, tend to prove that no alteration was necessary for the function of the bâtons percés in reindeer antler.
The difficulty of attaching yarn to the smooth reindeer antler bâtons, in addition to the shiny wear patterns observed on the sides of the holes observed in the experiment, led us to abandon the hypothesis of their use as torteiraes.
The apparent inability to lift even a tiny corner of the veil to try to unravel the mystery of these decorations thus remains. In the same way that it may seem easy to read the sign 'bison' although its meaning eludes us, so it was difficult to identify the 'ligature' symbol, and many schematic decorations escape our understanding.
While it is easy to imagine that there is probably no symbolism related to the 'ligature' symbol should we think that the 'bison' symbol engraved on a bâton percé is just a decoration?
The famous 'Laguiole' knives generally carry, near the joint, two motifs, contiguous when the knife is opened: on the handle, a bee, and on the blade, a series of alternating notches interpreted as a decoration associated with an abstract décor.
Photo: © K Sabatier
Source: http://www.sabatier-shop.com/2531-laguiole--laguiole-passion---carved-bee-by-hand----blond-horn.html
Text: Rigaud (2001)
But although the bee is a figurative representation and the symbolic emblem of 'Laguiole' knives, one is often unaware that the notches are not an abstract sign. They were originally intended to be struck by a flint to produce sparks, used to light a fire when combined with char cloth and kindling and some skill. Their origin is purely functional, but they remain only as a decoration without any symbolic connotation.
The two decorations, then, do not permit, neither the one nor the other, the understanding of their function on the knife.
Could this be the case for reindeer antler bâtons percés? As envisaged by J. Allain for harpoons, reindeer antler bâtons percés coexisted in a shape almost identical to wooden ones, but the wooden ones having not been preserved, and leaving no trace, some of these functional facilities linked to a specific use become optiional sets of the first.
A review of several 'phalluses', 'beaks' and 'fins' at low magnifications did not show wear concordant with their use as a decoration that nevertheless had a practical use. Only a thorough wear analysis could provide certainty, however.
( to rescue this hypothesis - Don ) Is there no cohabitation between two morphologically similar objects, one requiring a very durable material, reindeer antler for an unknown purpose, the other, wood, subjected to a lower stress as a torteira, intended for the manufacture of yarn and plied cord?
Men of the Upper Palaeolithic drew, painted and engraved realistic animals, but they also presented their works in a very schematic manner so that, often, we can see that they are at the ultimate level of abstraction.
'This duality of drawings is the same as that which appears in the elaborate characters of hieroglyphics or Chinese characters that have a cursive script for minor uses' (Leroi-Gourhan 1965).
A Magdalenian bâton percé from Laugerie-Basse has a representation of a very realistic ligature. Of the others, those at Isturitz or Gourdan show them schematically, from the everyday whipping used daily to fix the tips of spears to the shaft, to that for whipping the ends of ropes to stop them unravelling.
This idea is not new, but rather than bemoan the opacity of the signs we have tried to penetrate the vocabulary of the original rope-makers, assuming that they had experienced the same problems we had originally: to attach the cord to the bâton percé and then wind it onto the shaft.
Based on this assumption, we used the alterations and/or the following decorations related to winding problems of attachment and winding the cord onto the shaft:
Figure 18
A. Signs related to the windings:
A1, with contiguous parallel coils: strands, ligatures;
A2, cross-wound: various cross chevrons;
A3, changing the direction of winding: around the hole.
B. Signs related to adhesion problems on a naturally slippery material:
B1, groove, button, projection, and all signs called 'phallic' in general;
B2, beaks and tails; Signs related to winding problems: improvements avoiding the sliding of the cord on the barrel:
C1, cupules, notches;
C2, separation of the head and the shaft;
C3, transverse or oblique grooves. One object can have multiple decorations on both the head and the shaft.
Drawings: A Rigaud
Source and text: Rigaud (2001)
The three symbols associated with windings appear essentially to be decorations. Others appear to be related either to facilities for usages that escape us, or to useful changes which then become seen as decorations. The most controversial is undoubtedly the sign C3.
Concerning sagaies or spear heads, although we know the part embedded in the fitting, it is sometimes difficult to differentiate between striations for roughening to aid secure attachment, and those of a purely decorative nature.
For bâtons percés, the problem is much more complex, and we have grouped under this label a number of transverse or oblique grooves, but not longitudinal ones, which could facilitate the adhesion of a cord on the shaft.
Observations of 326 bâtons with a single perforation and 35 bâtons with two or more perforations were discussed in the work of Noiret (1990) From all the evidence, depending on the chosen criteria, bâtons with two or more perforations have totally different decorations from the others.
Virtually just one décor was used on the heads, the one which we have called 'around the hole' (A3), and only one is common on shafts, the apparent depiction of cross-wound spirals or chevrons (A2).
To conclude from these differences that these bâtons had a different function is a step that we will not cross. Regarding bâtons with but one hole, the problem is more complex.
Although the two preceding signs (A2 and A3) are found in significant quantities, the best-represented sign is the sign C3, which may mean simply that it covers, as we were discussing earlier, completely different categories. The frequency of Cl and C2 signs, however, tempers that remark.
Absent on the bâtons with several holes, the attachment signs Bl (phallus of all kinds) and C2 ( 'fins' and 'beaks') which together number 61, represent 31% of all combined signs.
Observed with an essentially practical perspective, these features/decorations appear sufficient to allow us to think, that although the torteiraes hypothesis is not plausible, that a relationship does exist between cords in general and bâtons percés.
Figure 20
Phallic bâtons percés from La Garenne.
Uniquely simple and functional in origin, these features/decorations, in their artistic context, were represented in many different ways within the same habitat, as evidenced by these two pieces from La Garenne, one very schematic, the other naturalistic, at left.
Photo and text: Rigaud (2001)
Conclusion on the current assumptions
Although we can straighten a spear head with a bâton percé, the straightening of spear heads does not necessarily require such an instrument, and the traces it might have left on the spear heads do not correspond to those observed.
Although a bâton percé can serve as the handle of a sling, we may as well throw a stone with an ordinary sling. As well, wear patterns observed by A. Glory as a result of his experiences are not a decisive argument.
It is possible to spin animal or plant fibres with a reindeer antler bâton percé, but the friction of the wood rubbing against the antler leaves a polish that is not observed on the prehistoric pieces. This last remark also confirms what we knew in advance about the use of bâtons percés to light a fire.
These four examples suffice to show that we do not yet know the true use of the bâton percé, and many authors, because they can not decide objectively the truth of the matter, admit, out of prudence, the possibility of multiple uses.
The carbon steel knife with a single blade is, par excellence, an almost universal tool to get out of many situations. It is able, amongst other uses, as well as to cut, which is its primary function, to scrape or scratch, open an envelope or a nut, strip electrical wire, tighten a screw or be used as a lever to open a jar.
Many knives have thus ended their lives during this last operation, with a broken blade caused by their use in a situation for which they were not designed. However, when looking at a collection of used knives, many are worn by repeated sharpening, some are chipped, but few are broken because the accident resulted from a secondary and infrequent use.
This is different for bâtons percés, since a large number have reached us broken in several places. The owner of a bâton percé, decorated as it was originally, thus knew well that eventually his tool would break because the purpose for which it was intended predestined it for this purpose.
To our knowledge, among the four examples above, no use can cause the breakage of a bâton percé, especially with such constancy, and we see ourselves forced to look for another possible use, a situation generating more fractures.
The breakage of reindeer antler
Three times already, we have published papers which addressed the problem of the fracture of fresh antler produced by an exaggerated flexion, whether deliberate or accidental: Allain et al (1985), Allain, Rigaud (1986), Rigaud (in preparation).
Figure 21 - Fractures of reindeer antler by bending
1a, 2a, 3a: Experimental pieces.
1b, 3b: Sagaies (spear heads) from La Garenne.
2b: Bâton percé from Laugerie Basse MH 1352.
4: End of the handle of a tool from La Garenne.
We hold, then, that there are two types of fractures which can be experimentally reproduced and compared with archaeological finds:
1: bevel or whistle fractures (Fig. 21, No. 3), which occur when the initial crack can develop in a straight line and at an angle, without being deflected by the presence of a link or a point pressing the edge of a block of stone, for example;
2: sawtooth breaks, short, occurring when the initial crack can not run straight. These breaks are characteristic of the bases of spears, and shuttles broken flush with the ligature. They are also frequent during the shaping of some antlers without sufficient preparation (fig. 21, Nos 1, 4).
Photo and text: Rigaud (2001)
Figure 22
Fractures of ciseaux or chisels: la, La Garenne; lb, accidental fracture during the course of the extraction of a baguette from reindeer antler.
2, La Garenne, pieces with double tongue characteristics, in particular, of the chisels fracture.
3, different theoretical phases of the fracture of a chisel, drawn by A. Rigaud.
Another fracture, often with 'ciseaux' or 'chisels' and spears, proved to be more common than we had thought, and then we had the chance to accidentally reproduce it by creating a baguette of reindeer antler (fig. 22, No. lb) .
Photo and text: Rigaud (2001)
In fact, there are two fractures whose origin is the middle of the curvature caused by the impact of the blow.
From this point, two divergent cracks arise that propagate obliquely when bending increased (Fig. 22 No. 3). In fact, the problem is complex. The fibres of the convex portion of the bend undergo elongation while at the same time, those of the concave portion are compressed.
When the three pieces separated after the breakage, we then noticed a small piece of subtriangular longitudinal section, which turns out to be entirely characteristic. (fig. 22, No. 2)
As part of a DEA, a Diplôme d'Études Appliquées, A. Legrand (2000) counted 10 similar pieces in the bone material of La Garenne. Bertrand (1999), meanwhile, found six: whistle or tongue, with central tongue, vertical, serrated or torn, level, skewed or oblique.
The visual documentation on which we worked is generally not precise enough to account for all of these categories.
Moreover, as regards the bâtons percés, the great interest in the nature of the fractures of the hole and the shaft is to make us aware of the direction of the force that caused the bending and fracture, because this force is always more or less perpendicular to the edge of the hole.
However, it is not always easy to determine exactly whether this force was facing up or down (fig. 21, No. 4), unless the antler has preserved the evidence of this bending. (fig. 21, No. 2a).
Fracture of Bâtons Percés
Figure 23
Bâtons à un seul trou - bâtons with one hole.
Bâtons à plusieurs trous - bâtons with two or more holes.
We have noted the different fractures contained in the diagrams of P. Noiret who postulated only three possibilities for fractures of the 'eyes' of the bâtons percés, in a study of 368 bâtons percés:
• perpendicular to the axis of the shaft (a1 and a2)
• obliquely to the axis of the shaft (b1 and b2)
• parallel to the axis of the shaft (c1 and c2); and five fractures of the shaft
• bevelled or sawtooth (d1, d2 and el, e2)
• by lateral flexion (d1 and e1)
• posterior anterior flexion (d2 and e2)
• steep indeterminate direction (f)
Photo and text: Rigaud (2001)
References
- Allain J., Descout J., 1957: A propos d'une baguette à rainure armée de silex découverte dans le Magdalénien de Saint-Marcel, L'Anthropologie, 61, 5-6, p. 503-512.
- Allain J. et al., 1985: Le Magdalénien à navettes, Gallia Préhistoire, 28, 1, p. 37-124.
- Allain J., Rigaud A., 1986: Décor et fonction, quelques exemples tirés du Magdalénien, L'Anthropologie, 90, 4, p. 713-738.
- Averbouh A., Begouën R., Clottes J., 1999: Technique et économie du travail du bois de cervidé chez les Magdaléniens d'Enlène (Montesquieu-Avantès, Ariège). Vers l'identification d'un cycle saisonnier de production, Préhistoire d'os. Recueil d'études sur l'industrie osseuse offert à Henriette Camps-Fabrer,Aix-en-Provence, Publication de l'Université de Provence, p. 289-318.
- Bertrand A., 1999: Les armatures des sagaies magdaléniennes en matière dure animale dans les Pyrénées, Oxford, BAR International Series, 773, 138 p., annexes.
- Bouchud J., 1954: Le renne au Paléolithique supérieur, Bulletin de la Société d'études et de recherches préhistoriques des Eyzies, 4, p. 17-20.
- Braun I., 2009: Die jungpaläolithische Kleinkunst in Mitteldeutschland, Praehistoria Thuringica, 12, S. 164-179 Langenweißbach 2009.
- Breuil H., 1954: Bâtons percés paléolithiques supérieurs et torteiraes (portugais), Chronique du IV congrès international des sciences préhistoriques et protohistoriques, Madrid, p. 207-210.
- Delluc B., Delluc G., 1979:L'Accès aux parois, in: Leroi-Gourhan A., Allain J. (éds), Lascaux inconnu, Gallia Préhistoire, MXIIe suppl., Paris, éd. du CNRS, p. 175-184.
- Glory A., 1959: Débris de corde paléolithique à la grotte de Lascaux (Dordogne), Mémoires de la Société préhistorique française, 5, p. 135-169.
- Glory A., 1961: La grotte de Rigney (Doubs), Bulletin de la Société préhistorique française, 58, p. 389-400.
- Glory A., 1965: Nouvelle théorie d'utilisation des bâtons percés, Centenaire de la Préhistoire en Périgord (1864-1964), Périgueux, Société historique et archéologique du Périgord, p. 56-62, suppl. au Bulletin de la Société historique et archéologique du Périgord, 91, 1964.
- Julien M., 1982: Les harpons magdaléniens, XVIIe suppl. à Gallia Préhistoire, Paris, éd. du CNRS, 291 p.
- Kilgore C., Gonthier E., 2014: Premières découvertes sur les techniques de fabrication de cordages àpartir de rouets (Bâtons-percés). Évidences sur le mobilier et l’art pariétal du Paléolithique supérieur (Magdalénien) First discoveries of cordage manufacture using perforated bâtons. Evidence from Upper Palaeolithic mobiliary and parietal art, L’Anthropologie, (2014), http://dx.doi.org/10.1016/j.anthro.2014.09.003
- Laurent G., 1911: Nouveau manuel complet du cordier, Paris, Paris, Encyclopédie Robert, p. 50-137.
- Leroi-Gourhan A., 1943: Evolutions et techniques -1- L'homme et la matière, Paris, Albin Michel, coll. Sciences d'aujourd'hui, 367 pp.
- Lompre A., 2003: Une nouvelle approche techno-fonctionnelle, Préhistoires Méditerranéennes, 12 | 2003, 147-163.
- Mons L., 1976: Les bâtons perforés de la grotte du Placard (Charente) au Musée des Antiquités nationales, Antiquités nationales, 8, p. 11-20.
- Nelson E., 1900: The Eskimo about Bering Strait, U.S. Government Printing Office, 1900 - Eskimos - 516 pages
- Noiret P., 1990: Le décor des bâtons percés paléolithiques, Liège, Préhistoire liégeoise ASBL, 25, 2 vol. (vol. I: texte, 319 p. et catalogue, 227 p., 378 ill.; vol. II: planches, 215 pl.).
- Ochoa B. et al, 2020: Un baston multiperforado de la ocupacion del Magdaleniense Final de la cueva Aizkoltxo (Mendaro, Gipuzkoa), Complutum, Vol. 31, Issue 2, Complutense University of Madrid.
- Peltier A., 1992: Bâtons percés, baguettes, Camps-Fabrer H. (éd.), Fiches typologiques de l'industrie osseuse préhistorique, Cahier V-1.0., 1.1., 1.2., 1.3., bâtons percés, baguettes, Commission de nomenclature sur l'industrie de l'os préhistorique, Union internationale des sciences pré- et protohistoriques, Treignes, CEDARC, p. 7-64.
- Peltier A., 1992: Bâtons percés, baguettes, Camps-Fabrer H. (éd.), Fiches typologiques de l'industrie osseuse préhistorique, Cahier V-1.0., 1.1., 1.2., 1.3., bâtons percés, baguettes, Commission de nomenclature sur l'industrie de l'os préhistorique, Union internationale des sciences pré- et protohistoriques, Treignes, CEDARC, p. 7-64.
- Rigaud A., 2001: Les bâtons percés : décors énigmatiques et fonction possible, Gallia préhistoire, tome 43, 2001. pp. 101-151.
- Rigaud A., 2004: Usures expérimentales sur quatre bâtons percés utilisés comme bloqueurs de câble, Gallia préhistoire, tome 46, 2004. pp. 155-169;
- Vesilind P., 2000: Sur la piste des Vikings, National Geographic,France, 2.5, n° 8, p. 2-27.
- White R., 1986: Life in Ice Age Europe. Dark Caves, Bright Visions, New York, American Museum of Natural History, 176 p.